Французскі інстытут сонечнай энергіі INES распрацаваў новыя модулі PV з тэрмапластыкай і натуральнымі валокнамі, якія знаходзяцца ў Еўропе, напрыклад, ільняным і базальта. Навукоўцы імкнуцца знізіць экалагічны след і вагу сонечных батарэй, адначасова паляпшаючы ўтылізацыю.
Перапрацаваная шкляная панэль спераду і бялізну на задняй частцы
Выява: GD
З часопіса PV France
Даследчыкі Нацыянальнага інстытута сонечнай энергіі Францыі (INES)-аддзел Французскай альтэрнатыўнай энергіі і камісіі па атамнай энергіі (CEA)-распрацоўваюць сонечныя модулі, якія прадстаўляюць новыя біялагічныя матэрыялы ў пярэдняй і задняй баках.
"Паколькі выкіды вугляроду і аналіз жыццёвага цыклу сталі асноўнымі крытэрыямі ў выбары фотаэлектрычных панэляў, пошук матэрыялаў стане важным элементам у Еўропе ў бліжэйшыя некалькі гадоў",-сказаў Аніс Фуіні, дырэктар CEA-INES , у інтэрв'ю PV Magazine France.
Каардынатар даследчага праекта Aude Derrier заявіла, што яе калегі разгледзелі розныя матэрыялы, якія ўжо існуюць, каб знайсці той, які можа дазволіць вытворцам модуляў вырабляць панэлі, якія павышаюць прадукцыйнасць, даўгавечнасць і кошт, пры гэтым зніжаючы ўздзеянне на навакольнае асяроддзе. Першы дэманстратар складаецца з сонечных элементаў гетерозункцыі (HTJ), інтэграванага ў усеагульны матэрыял.
"Пярэдняя бок выраблена з палімера, напоўненага шкловалакна, які забяспечвае празрыстасць",-сказаў Дэрыер. "Задняя частка выраблена з кампазіта на аснове тэрмапластыкі, у якіх было інтэгравана ткацтва двух валокнаў, лёну і базальту, што забяспечыць механічную трываласць, але і лепшую ўстойлівасць да вільготнасці".
Ільно атрымана з Паўночнай Францыі, дзе ўжо прысутнічае ўся прамысловая экасістэма. Базальт знаходзіцца ў іншым месцы Еўропы і сплецены прамысловым партнёрам Інеса. Гэта знізіла выкіды вугляроду на 75 грамаў CO2 на ват, у параўнанні з эталонным модулем адной магутнасці. Вага таксама была аптымізавана і складае менш за 5 кілаграмаў на квадратны метр.
"Гэты модуль накіраваны на PV і інтэграцыю на даху", - сказаў Дэрыер. "Перавага заключаецца ў тым, што ён натуральна чорны колер, без неабходнасці ў спіне. З пункту гледжання перапрацоўкі, дзякуючы тэрмапластыцы, якія можна перарабіць, аддзяленне слаёў таксама тэхнічна прасцей ".
Модуль можа быць выраблены без адаптацыі бягучых працэсаў. Дэрыер сказаў, што ідэя заключаецца ў перадачы тэхналогіі вытворцам без дадатковых інвестыцый.
"Адзіны імператыў-мець маразільныя камеры для захоўвання матэрыялу, а не для запуску працэсу сшывання смалы, але большасць вытворцаў сёння выкарыстоўваюць Prepreg і ўжо абсталяваны для гэтага",-сказала яна.
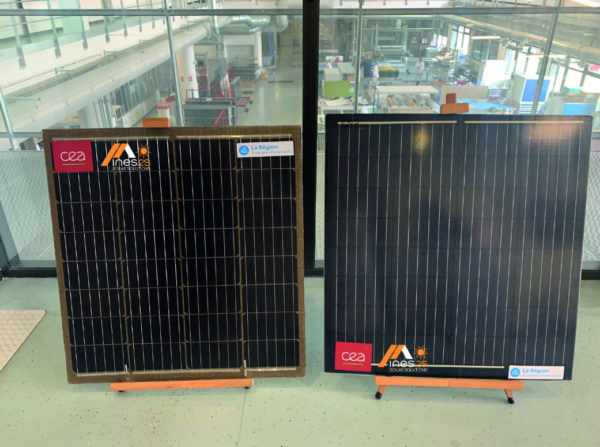
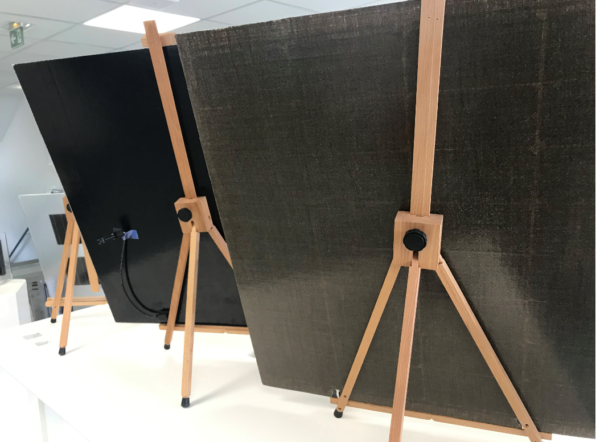
"Мы працавалі над другім жыццём шкла і распрацавалі модуль, які складаецца з паўторна выкарыстанага 2,8 мм шклянкі, які паходзіць са старога модуля", - сказаў Дэрыер. "Мы таксама выкарыстоўвалі тэрмапластычны інкапсулянт, які не патрабуе сшывання, які, такім чынам, будзе лёгка перапрацаваць, і тэрмапластычны кампазіт з ільняным валакном для супраціву".
Задняя частка модуля без базальта мае натуральны колер бялізны, які можа быць эстэтычна цікавым для архітэктараў з пункту гледжання інтэграцыі фасада, напрыклад. Акрамя таго, інструмент разліку INES паказаў на 10% зніжэнне выкідаў вугляроду.
"Цяпер неабходна ставіць пад сумнеў фотаэлектрычныя ланцужкі паставак", - сказаў Жуні. "З дапамогай рэгіёну Rhône-Alpes у рамках Міжнароднага плана развіцця мы пайшлі шукаць гульцоў за межамі сонечнага сектара, каб знайсці новыя тэрмапластыкі і новыя валокны. Мы таксама думалі пра бягучы працэс ламінавання, які вельмі энергарэгістраваны ".
Паміж ціскам, націскам і фазай астуджэння, ламінацыя звычайна доўжыцца ад 30 да 35 хвілін, пры працоўнай тэмпературы каля 150 С да 160 С.
"Але для модуляў, якія ўсё часцей уключаюць экалагічныя матэрыялы, неабходна пераўтварыць тэрмапластыку прыблізна ад 200 С да 250 С, ведаючы, што тэхналогія HTJ адчувальная да цяпла і не павінна перавышаць 200 С",-сказаў Дэрыер.
Даследчы інстытут аб'ядноўваецца з спецыялістам па тэрмакампрэсіі на аснове Францыі Roctool, каб скараціць час цыкла і вырабляць формы ў адпаведнасці з патрэбамі кліентаў. Разам яны распрацавалі модуль з заднім тварам, вырабленым з поліпрапіленавага тыпу тэрмапластычнага кампазіта, да якога былі інтэграваны перапрацаваны вугляродны валокны. Пярэдняя частка выраблена з тэрмапластыкі і шкловалакна.
"Працэс індукцыйнага тэрмакампрэсіі Roctool дазваляе хутка нагрэць дзве пярэднія і заднія пласціны, не дасягаючы 200 С у аснове клетак HTJ", - сказаў Дэрыер.
Кампанія сцвярджае, што інвестыцыі ніжэйшыя, і працэс можа дасягнуць часу цыкла ўсяго за некалькі хвілін, выкарыстоўваючы менш энергіі. Тэхналогія накіравана на кампазітных вытворцаў, каб даць ім магчымасць вырабляць часткі розных формаў і памераў, адначасова інтэгруючы больш лёгкія і больш трывалыя матэрыялы.
Час пасля: чэрвеня-24-2022